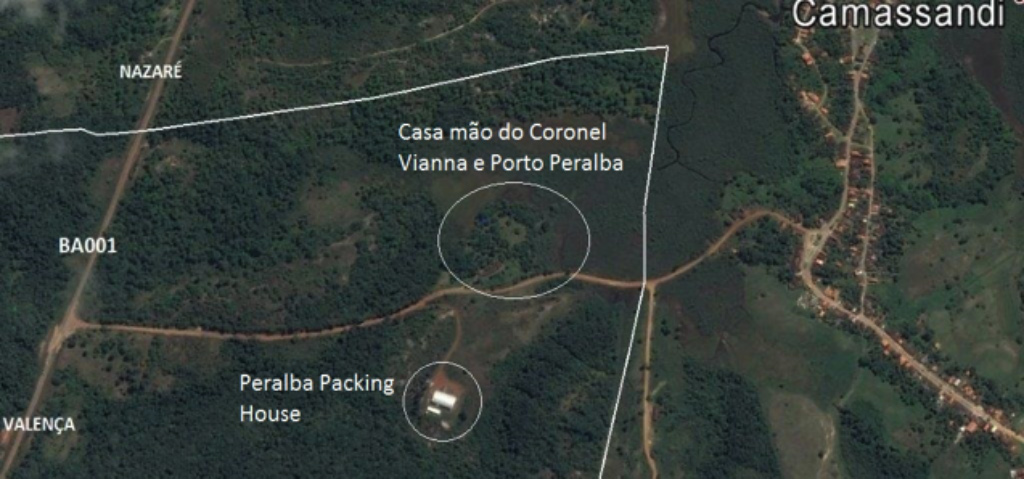
In 2010 our Dutch partners decided that we had to have our own packinghouse.
For three years, we rented the packingfunction in Cruz das Almas and Mangabeira, but the process was laborious and ran afoul of our control. Our Dutch partner wanted a CAT 1 + product, higher than most fruits exported in theworld, so that they could get a premium on sales and guarantee continuous sales: it was a tall order demand that we had to take on!
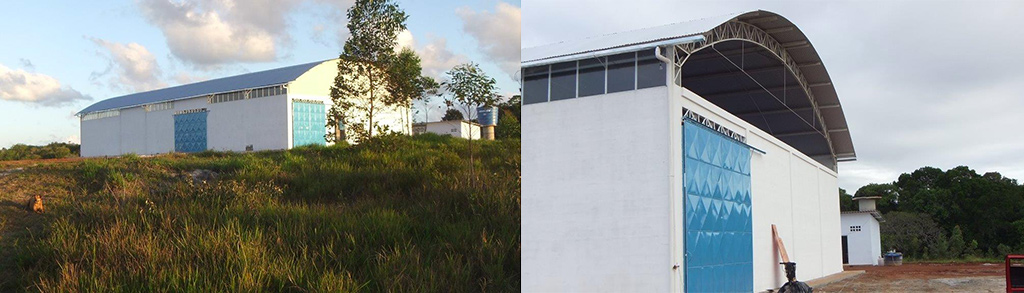
Just looking for the right place proved to be complex. With 30 to 40 tons trucks of refrigerated containers moving up and down untarred roads, we had to think carefully where to placethe packinghouse. After long discussions and investigations, involving our suppliers of reefers and trucks, we reached the decision to put the packing house400 meters off the BA001, a bit off from theplantation, but extremely accessible by the main road..
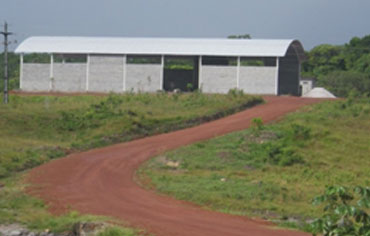
With the village of Camassandi close enough, we were also assured of easy access tolabor. Negotiations with the elders of the village made it easy and opened the road to a partnership that lasts until today. Within eight months, we built the most modern and well-conceived processing plant on the northeast of Brazil.
Immediately we created two brands: the Forest Green for CAT 1 ‘ normal ‘ and Peralba, for CAT 1 +, for an even more demanding market.
And we designed a new type of carton that would increase the number of boxes shipped in one container by 18%. In addition to our cartons being made with material much more resistant and resilient to the moisture that accumulates over the 12 days of crossing the sea to get to Salvador to Rotterdam, it was already approved by the European authorities for use with products for human consumption.
This carton cannot be produced in Brazil and so we had to import it on a drawback basis. But the most important aspect of this design is that European supermarkets prefer (and some even ask for) this box model because, in addition to its intrinsic qualities of design, clarity of images, presentation, resistance to handling, good presentation of the fruit, can be put directly on shelves and presented to the public as a special item.
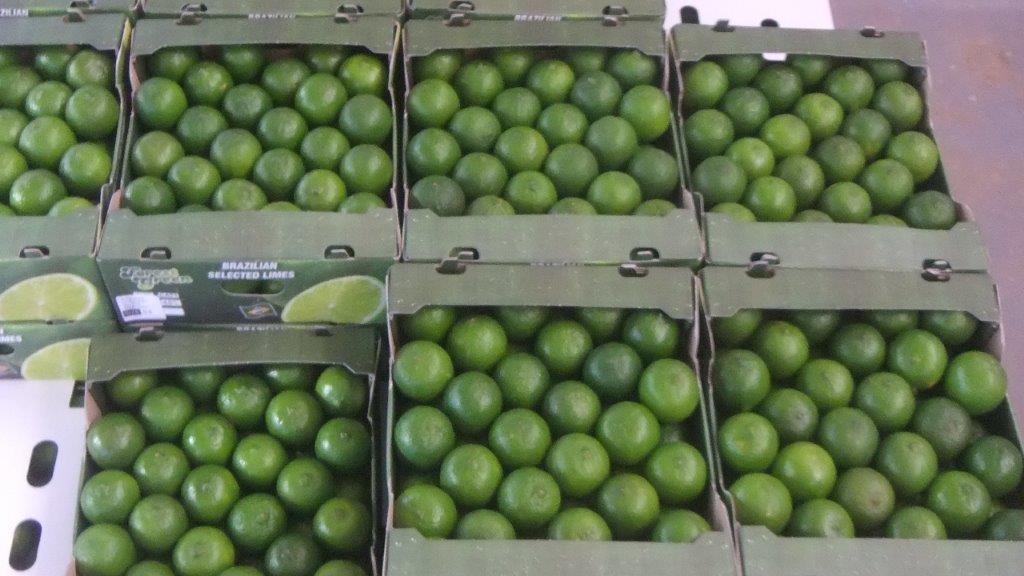
For us also this solution became very attractive because of its ease of handling by the packing girls. All the extra costs and hassles involved in the drawback process were well compensated by this one aspect alone!
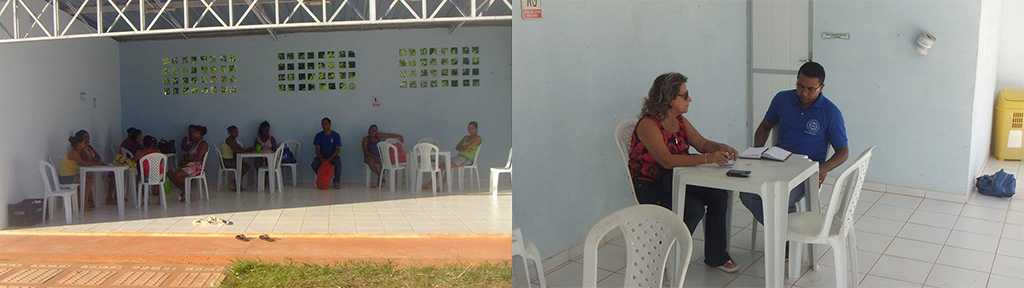
Despite all these pros and cons, the experience over the years demonstrated the value of designing a special carton. The most evident is that we can pack in a refrigerated container 6048 up to a maximum of 6336 boxes instead of usual 5240, the maximum number that we could pack if we used boxes produced in Brazil. Those 13% to 17% in the number of boxes being shipped in each container delivered makes a big difference at the end of the year.
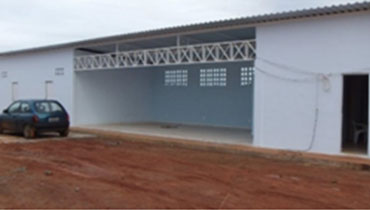
Then we took greatpains to provide comfortable working conditions for our staff. We made premises with separate bathrooms, infirmary, change of clothes room, dining room with fridge and stoves to warm up food, decontamination room. Even a small office. And we introduced ongoingtraining on basic cleaning and sanitation practices, including read and writing skills.
We bought machines that, at the time, were the most modern available in Brazil. Then placed two cold rooms of 80 m2 each, drilled an artesian well to ensure clean water, install an emergency generator of 30 KV, build a sewage and environmental purification system and linked the packing to the main electricity net.
And all, of course, in accordance with the GlobalGAP rules! wWith the 32 operators, we started to train in the selection and packaging of fruit for export. Not an easy task in the beginning.
Who know the rules of the GlobaGAP knows exactly what it all means: absolutely clean floors, smooth working machines, clean clothes, washing of hands, grooming of hair, fingernails, rings…
And also new working practices: change of clothes, entries in the packing always after disinfection of hands and feet, visits to services with dual disinfection of hands and feet, use of gloves, caps, uniforms, shoes, timetables, and on… it was not easy!
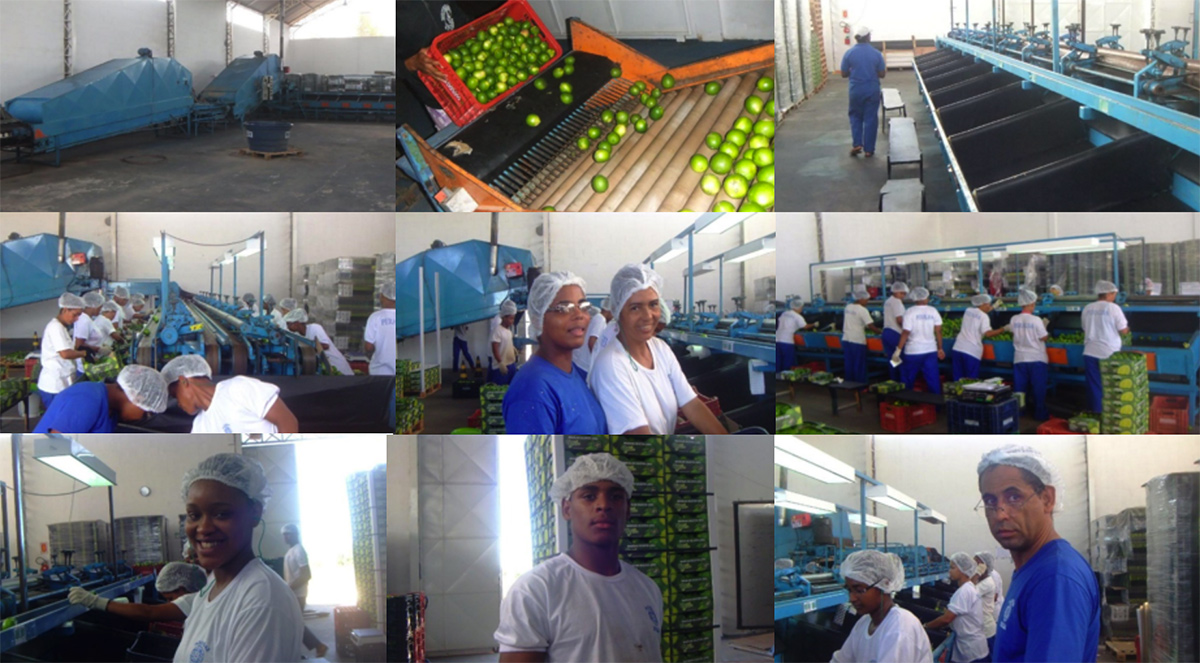
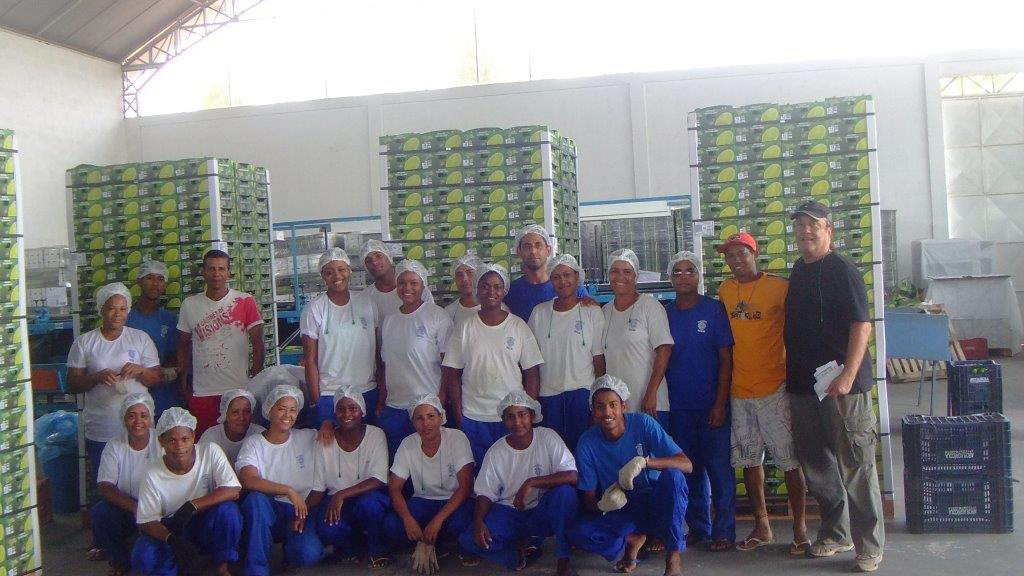
For us who were not used to these practices, was quite a lesson … But our efforts were well rewarded: today we have a fully dedicated and trained team with a high level of efficiency and effectiveness. In the opinion of many ‘experts’ in this type of operation, we are working well above national average.
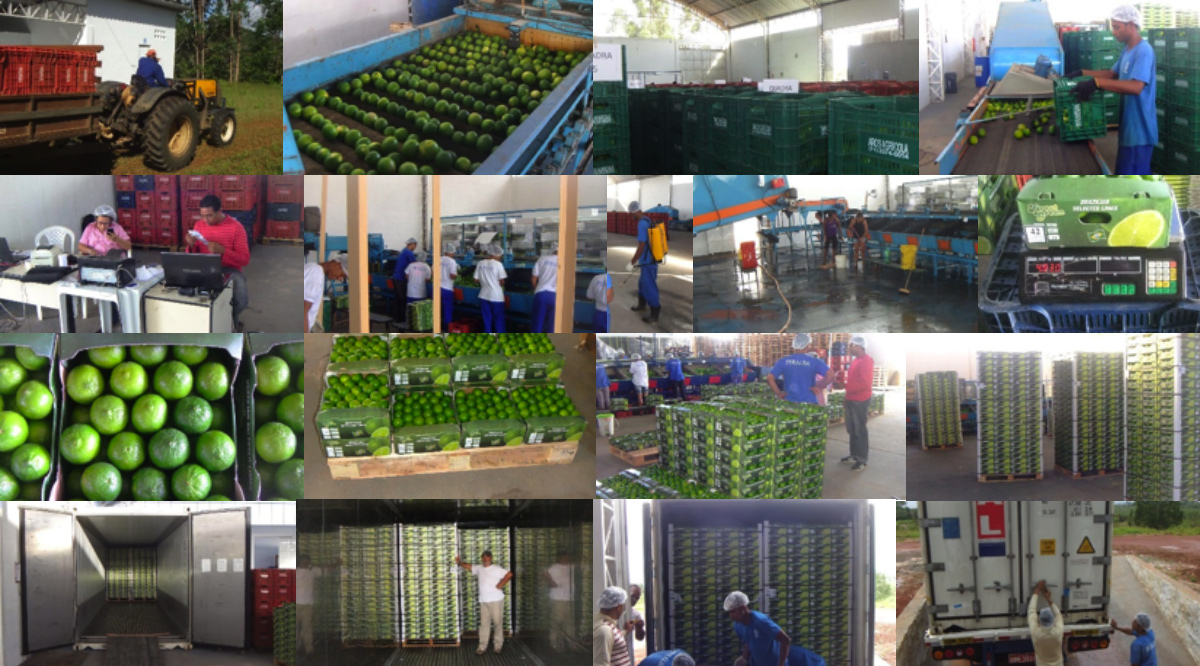